Introduction
In corrosion prevention by anti-corrosion coatings, three main principles are employed in various combinations:
- Create a barrier that keeps out charged ions and retards the penetration of water and oxygen.
- Ensure contact between the steel and a less noble metal (e.g. zinc in the coating) provides cathodic protection of the steel utilizing the galvanic effect.
- Ensure that water on its passage though the anti-corrosion coating takes on special properties or compounds inhibiting its corrosive action.
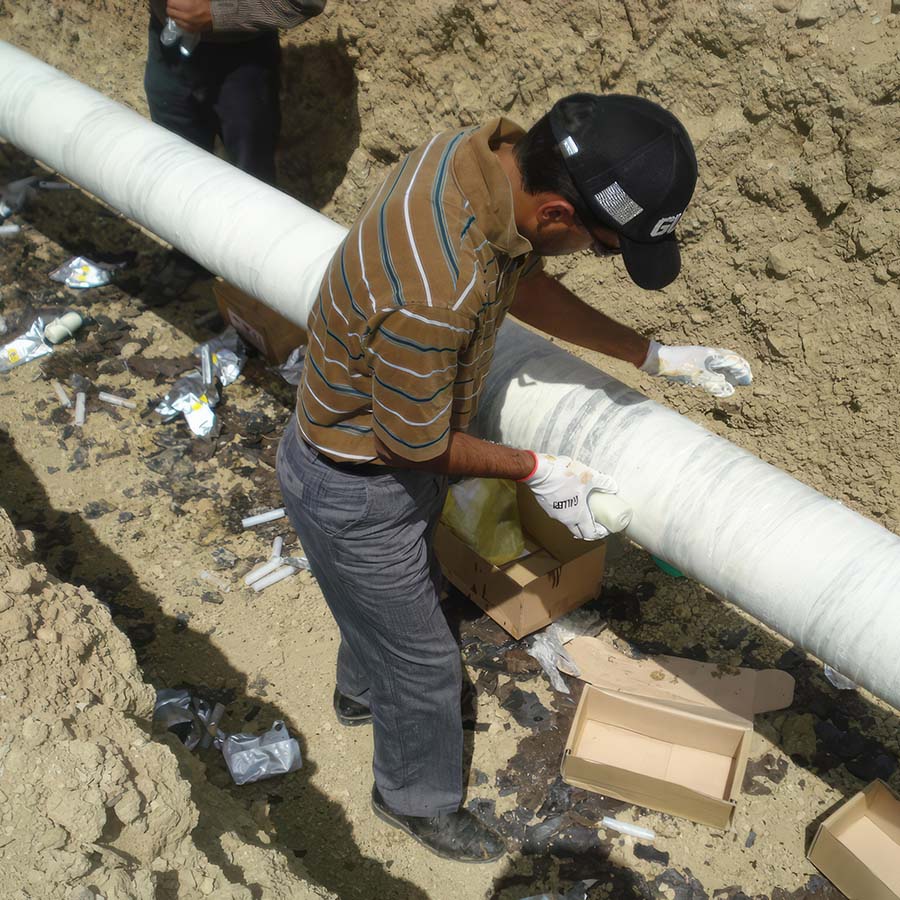
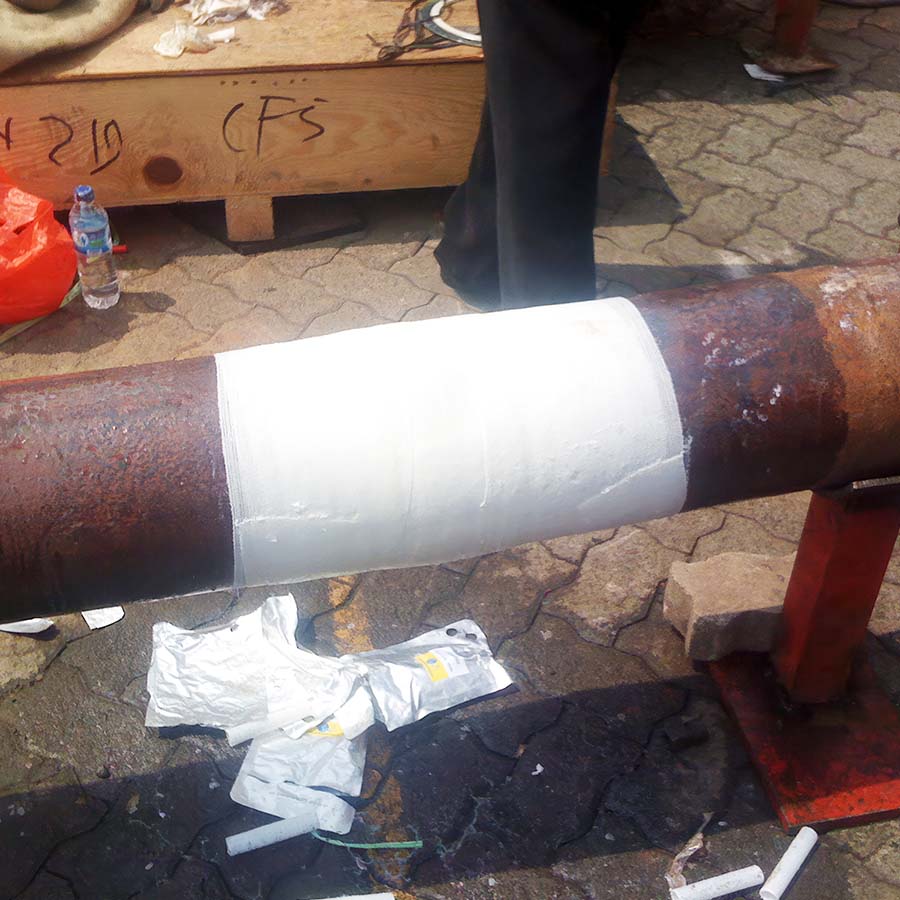
Barrier effect
The barrier effect may be obtained by applying a thick anti-corrosion coating, typically 200 to 350 microns. This barrier effect is the most commonly used type of anti-corrosion mechanism. Typical anti-corrosion coatings employing this mechanism include epoxies and polyurethanes. By adding flake pigments, such as leafing aluminum, an improved barrier effect can be achieved. The flake pigments are oriented parallel to the steel surface and water trying to pass through encounters a more complicated and longer passage around the pigment particles. For permanently immersed steel, the first and often the only choice in anti-corrosion coating protection is to utilize the barrier effect. However, if a barrier of the anti-corrosion coating is damaged, the damaged area is open for corrosion to begin. Corrosion can then proceed into the steel substrate and outwards under the intact anti-corrosion coating, known as rust jacking or under film rusting. Where there is a risk of mechanical damage, additional protection such as cathodic protection is sometimes provided.
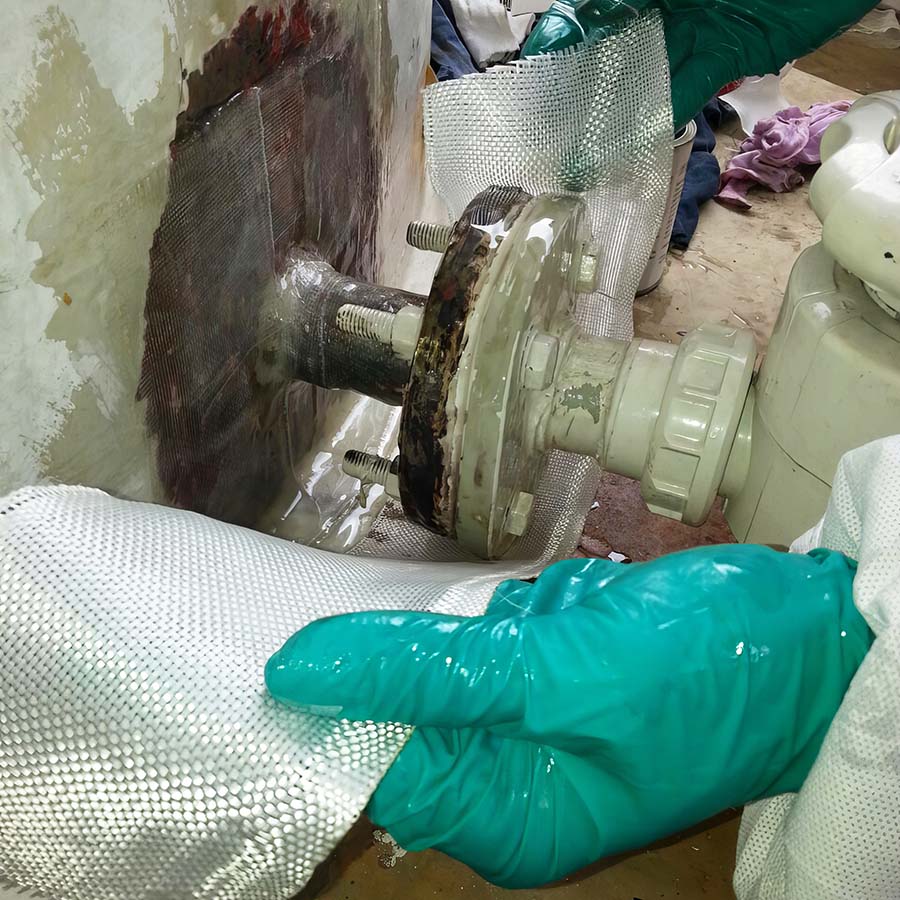
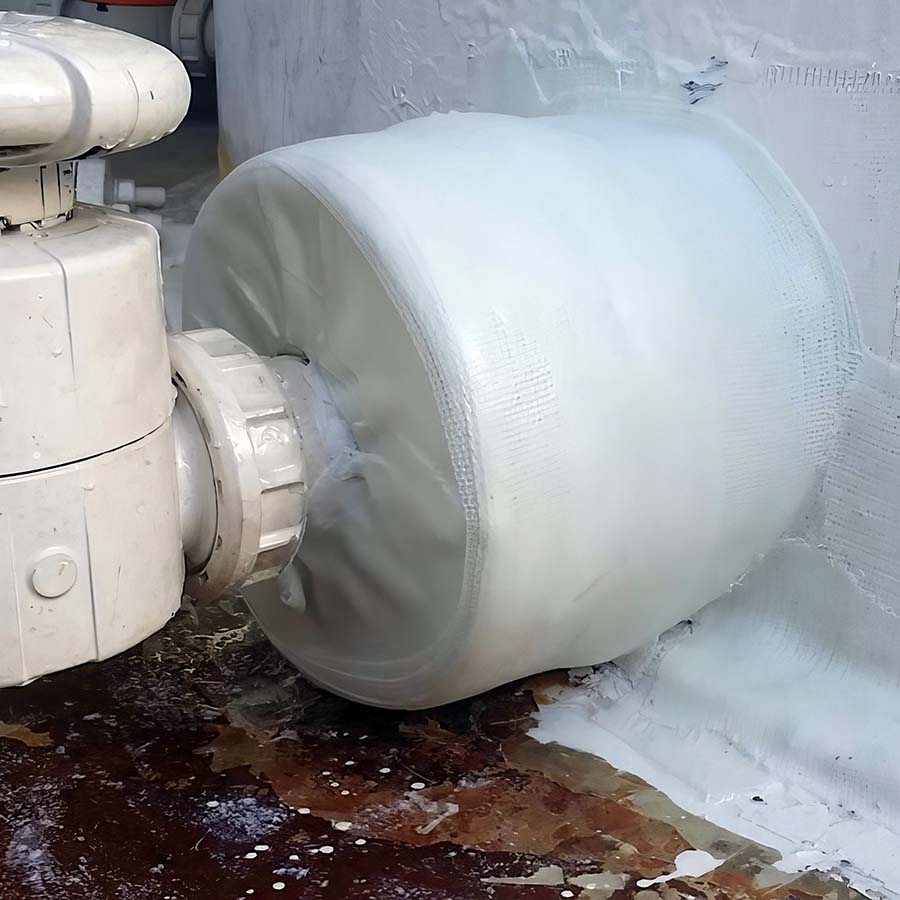
Galvanic effect
Protection of steel through the galvanic effect (cathodic protection) can be achieved with coatings containing large amounts of metallic zinc or aluminum. A condition for effective protection is that the anti-corrosion coating is formulated to give metallic contact between the individual metal pigment particles and between these particles and the steel. The very nature of these coatings requires an absolutely clean steel surface and, especially for zinc silicates, a well-defined surface profile for a lasting coating system. When applied, zinc silicates are initially porous. After a while the porosity is filled with corrosion products from the zinc and a barrier is formed. When damaged, the galvanic effect is re-established at the damaged area and the steel is protected effectively against rust creeping.
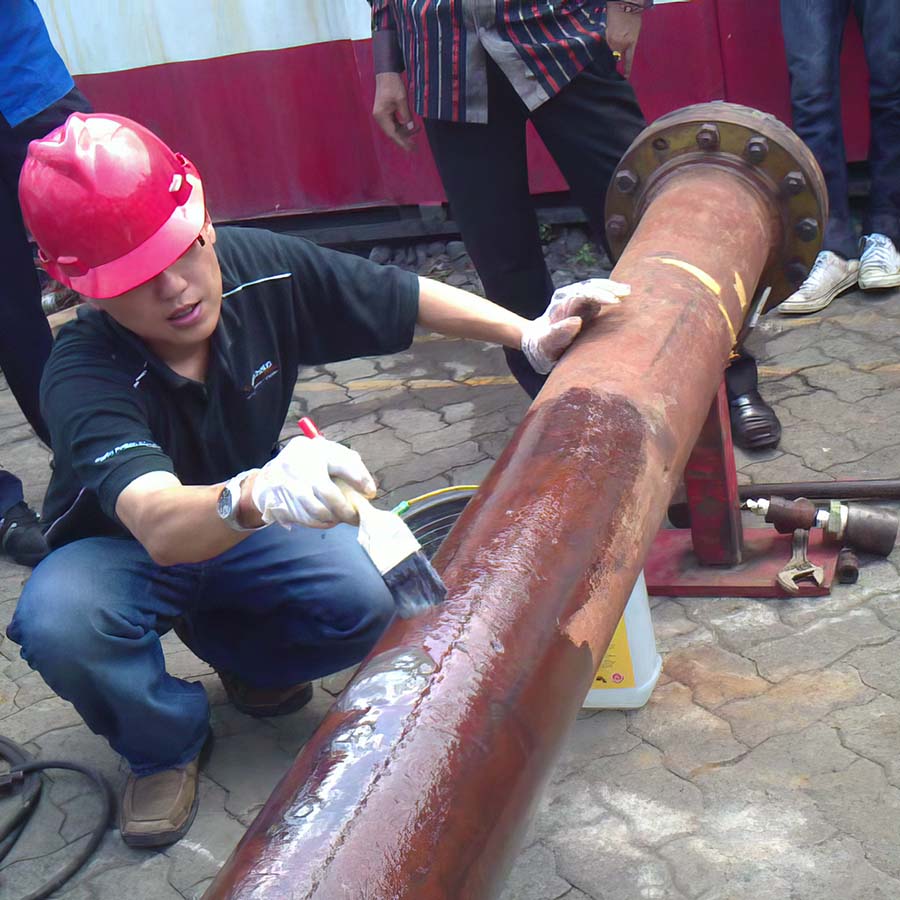
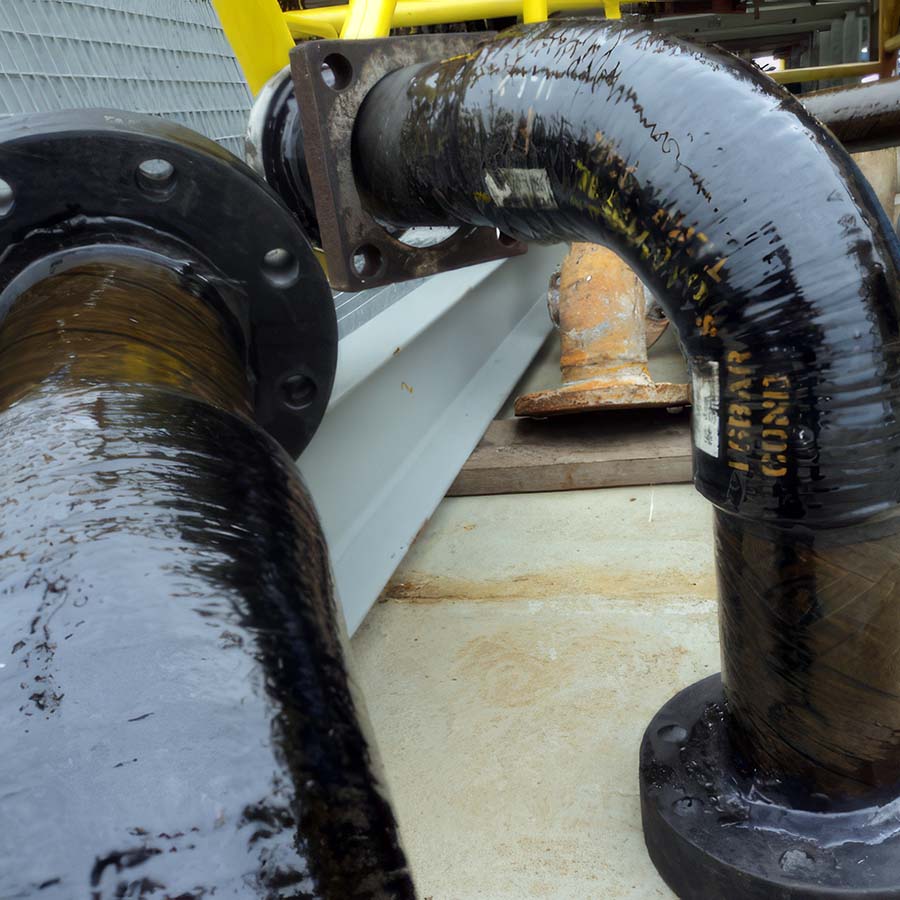
Inhibitor effect
A corrosion-inhibiting effect is achieved by using primers containing inhibitors. These are soluble or basic pigments designed to suppress the corrosion process. Inhibitors work by reducing the rate of either the anodic or the cathodic process, or by depositing a high resistance film onto the corroding surface. The corrosion current flowing between the anodic area and the cathodic area is usually reduced by at least an order of magnitude. To prevent them from being washed out of the primer coats, top coats without inhibitors are applied to provide the barrier necessary for the inhibitive primer to last. However, due to the water solubility of the pigments used, inhibitive primers are not suited for prolonged immersion, as they suffer from blistering and subsequent early breakdown of the anti-corrosion coating system can occur. When damaged, reasonable protection against rust creeping or under rusting is provided if the damaged area is not too large. When the inhibitor has been used up, corrosion will occur.
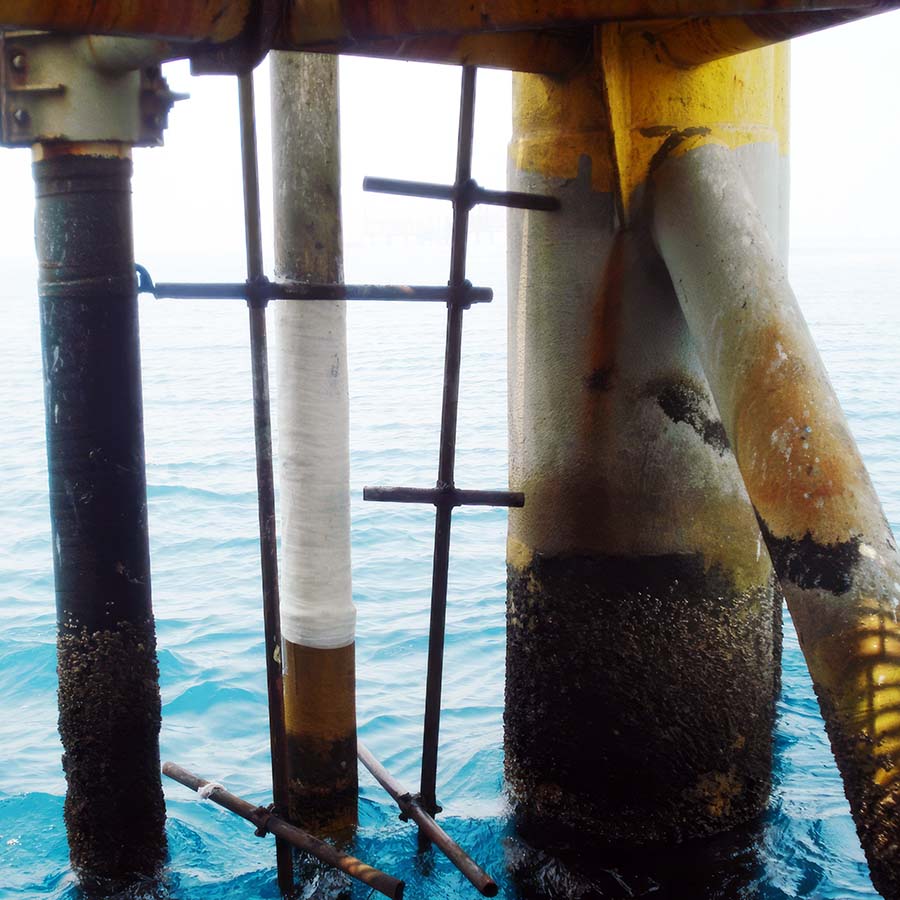
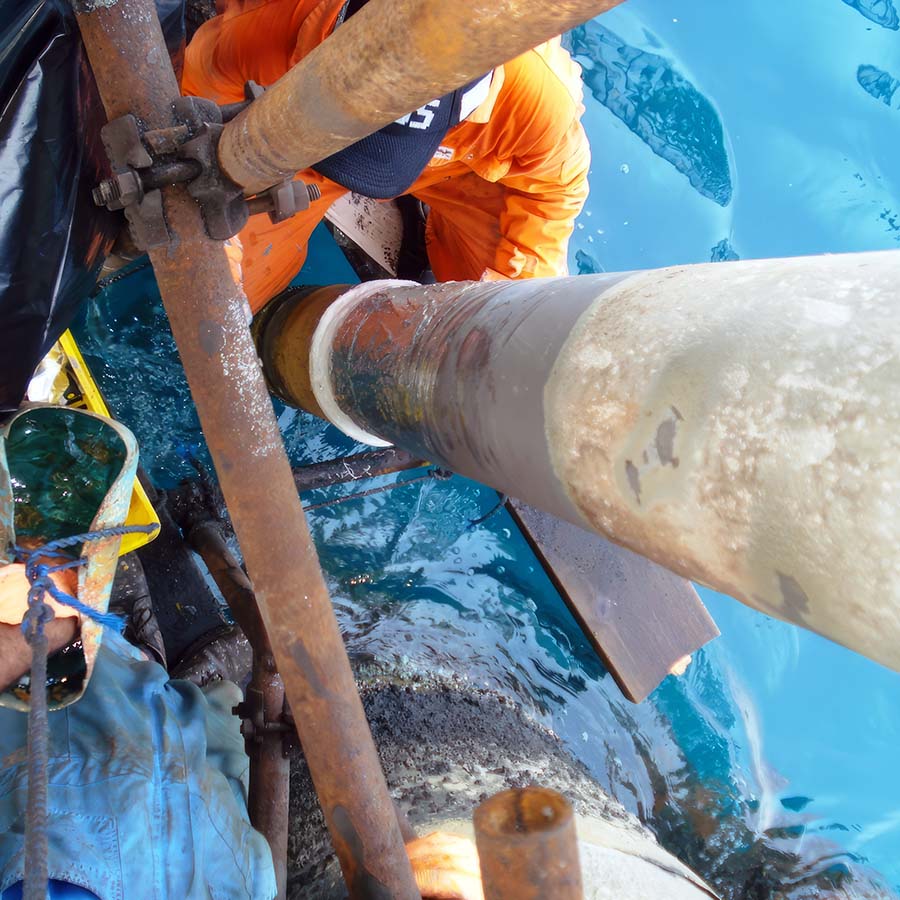
Surface tolerant coatings
After a vessel enters service, corrosion will begin to occur under coatings in cargo tanks and holds at areas of damage or at regions where good surface preparation was not initially carried out. Maintenance of the anti-corrosion coating is essential if its target service life is to be achieved. Any damages to the anti-corrosion coating or any areas of rust jacking must be repaired as quickly as possible. Under service conditions, it is not always possible to achieve a very high standard of surface preparation, although some vessels have small scale abrasive blasting equipment on board. The application of surface tolerant anti-corrosion coating products can be useful in the repair coating process. However, it should be remembered that no paint will perform adequately if it is applied onto heavily rusted or contaminated surfaces and that steel preparation should always be carried out to the proper or highest possible standards, to avoid the necessity to repair the same area many times. Outer hulls of vessels suffer from mechanical damage from fendering, tugs, etc., and with time, this can result in pitted steel which is difficult to clean by spot abrasive blasting. The steel looks clean visually but ionic contaminants, such as salts, can be trapped under rust scales or in pits. Washing the surface with fresh water can help to reduce the residual contamination. The use of surface tolerant anti-corrosion coatings in this situation can also be beneficial, providing that the levels of contamination are not excessive.

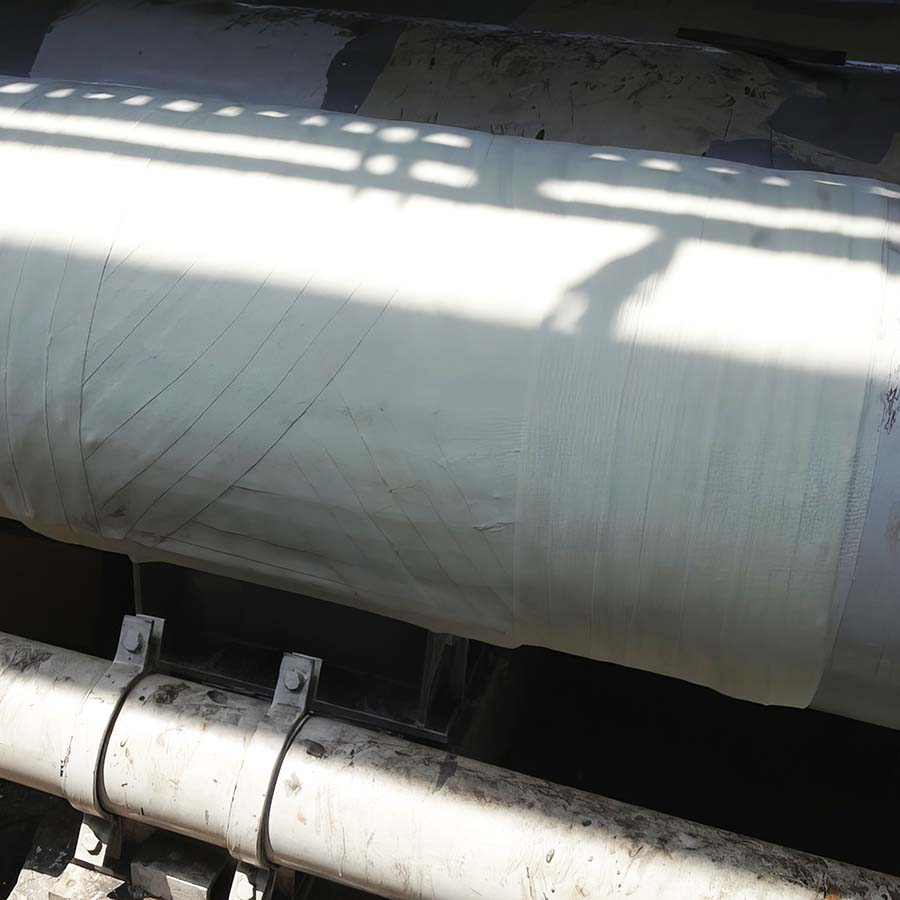
Anti-corrosion coating compatibility
Anti-corrosion coatings such as epoxies have very specific over-coating time intervals (sometimes called the over-coating window) and these times must be strictly followed if the individual layers are to adhere to each other.
Anti-corrosion coating compatibility is also important when maintenance and repair work is carried out, to ensure that the repair coat will adhere to the original coatings, or failures will occur between the individual layers (inter-coat adhesion failure).
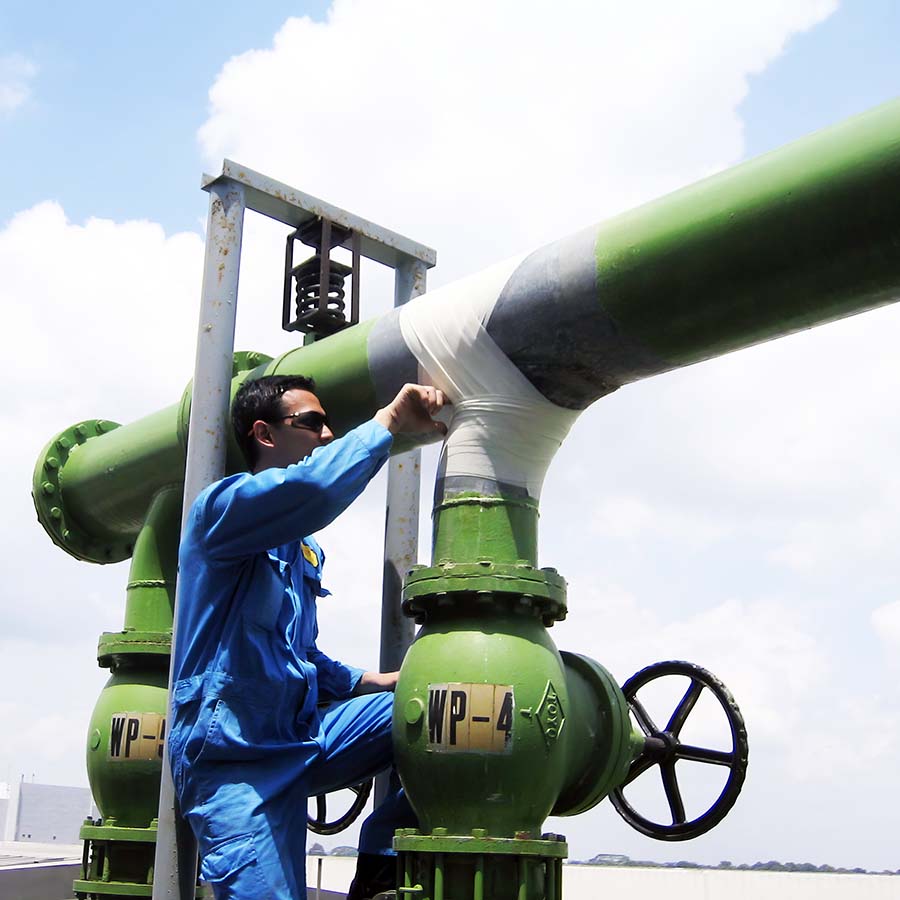
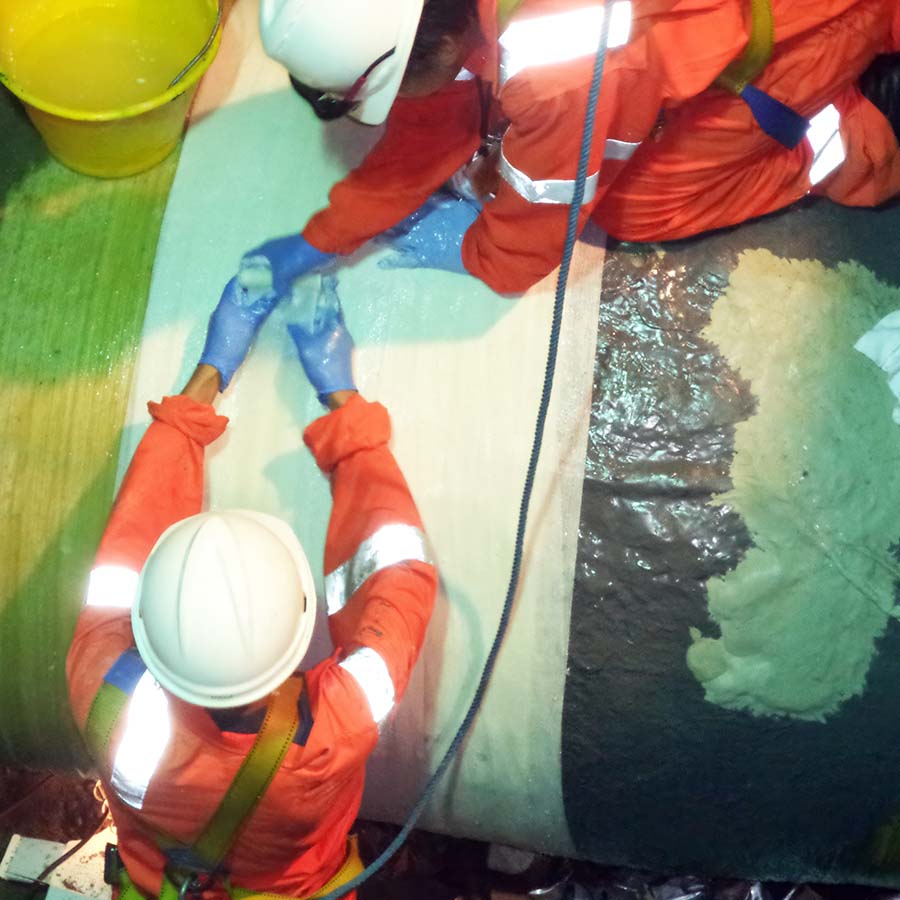
Stripe coats
Stripe coats are generally applied during the new building process as the blocks are being coated. They are also applied during maintenance and repair/refurbishment. Spray application processes and the inherent nature of paints in the liquid state cause the anti-corrosion coating to pull back from sharp edges and this results in the formation of a thin film at edges.
For ballast tanks, a second scheme coat and a second stripe coat will be added. The purpose of the stripe coat is to add an extra thickness (preferably about 30 microns) of anti-corrosion coating around vulnerable areas such as cut edges, welds and drain holes. During routine maintenance on board the vessel, the application of stripe coats during repair work (particularly if the vessel was constructed without stripe coats) will prolong the life of the anti-corrosion coating scheme.